Shandong West Glass Products Co., Ltd.It is a company specializing in the production and research of new materials such as Smart Film / Glass / Automotive Film / Home & Office Window Film and Special Functional Film etc.
After 5 years of exploration,the level is also increasing. In the process of construction, we have encountered various thorny problems. While helping customers solve difficulties, we have also continuously improved our comprehensive quality and accumulated valuable experience. In order to promote the development of the PDLC film industry, our company summarizes the problems that are prone to occur in the construction process of the PDLC film, analyzes specific classic cases, and provides solutions.
Problems Overview
1、Production Process Reasons
2、Construction Link Reasons
3、Link Of Raw Materials Reasons
4、Operation Link Of Business Personnel Reasons
5、Customer Factor Reasons
Production Process Reasons
Problem 1:Smart film not work ; or after installation for a period, suddenly not work.

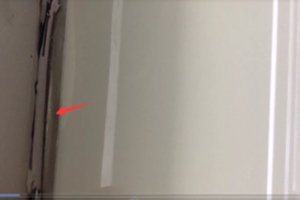
Reason:
1.After making the busbar, wipe the liquid crystal too heavy,resulting in excessive ITO resistance. After working for a long time,the ITO conductive layer is burned and the film cannot work
2.The content of conductive silver powder in the glue on the back of the electrode is not high, and the contact with ITO is not enough; the welding busbar position is loose and the conductivity is weak, resulting in poor contact.
3.The waterproofing of the busbar position is not done well. After a long time working, water vapor intrusion, and poor contact due to weak conductivity.
Other Site Reasons:
1.Power , remote, wire, site environment have problem.
2.Busbar or wire contact the profiles and cause short circuit.
3.Site cutting, There are burrs around the membrane, which lead to short circuits at the corners after power-on.
4.Corrosion and oxidation of busbar in high temperature and high humidity environment, resulting in poor contact.
Solution:
1.Strengthen the training and testing of liquid crystal wiping. At the same time, ITO resistance needs to be tested and backup test data before leaving the factory.
2.Adjust the electrode production method, use copper mesh instead of copper foil as the busbar, to increase the contact area between the copper mesh and the ITO conductive layer, thereby increasing the conductivity.
3.Apply waterproof glue on the electrode position and around the membrane, and bake in the oven to remove the moisture on the membrane surface and around it.
Effect Feedback:
After 3-6 months of testing, so far, the film using the copper mesh as the busbar has not shown that the film is not bright.
Problem 2:Smart film not work .


Reason:
During busbar making, because welding way not right, so cause busbar loose.
Solution:
1.Adjust busbar making way- copper net.
2.Have relevant training regularly.
3.Enhance checking strength.
Problem 3:Smart film has impurities


Reason:
1.Dust mark: The cloth under the film when the film enters the oven .There is dust, the dust sticks to the surface of the film when the oven is heated, and dust marks appear.
2.Paper scraps: replace the label paper, but it is not cleaned up.
3.There are gray spots, white spots and other impurities on the raw material itself failed to detect.
Solution:
1.The workshop is hygienic and clean to reduce dust;Make sure the place where the Fabric is placed is clean and tidy.
2.Check that the surface of the fabric is smooth.
3.Shake the fabric slightly when it is placed in the oven.
4.Strengthen workshop quality inspection.
Problem 4:There are burning spots on the film.


Reason:
1.When scraping the copper foil with a scraper for making busbar, uneven force, then copper foil gets damaged. When at power on state, would be burnt and have these spots.
2.Test voltage: the film is energized test, due to the instability of the voltage.Causes that film damaged and have these burnt spot.
confirm that there is no defect, and then package and ship.
Other Reasons:
1.The busbar edge contacted with the mounting profile, resulting in a short circuit, which in turn causes the film to have burning spots.
2.Metal dust in the air contacted the busbar position and caused a short circuit, which in turn causes the film to have spots.
3.The water vapor in the air is immersed around the film, resulting in a short circuit.
Solution:
1.Personnel making electrodes should pay attention to the details and force of making the membrane.
2.The test people need to ensures that the test voltage is stable and recheck the surface of the film.
Problem 5: Imprints.
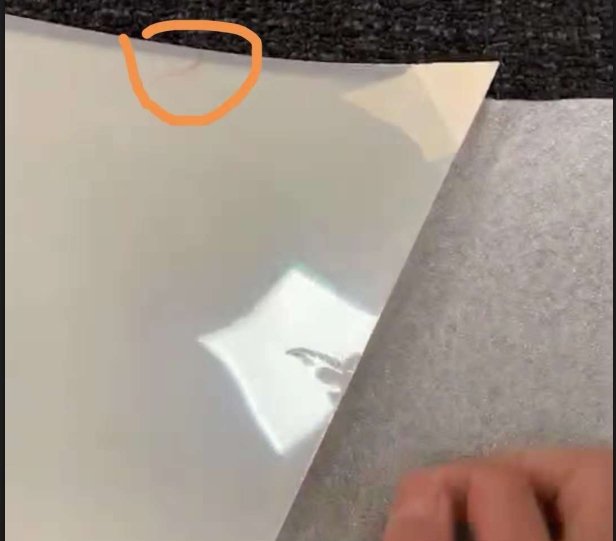
Reason:
1.There is a uniform grain, and the roll film is too close to the roll during packaging, resulting in indentation.
2.Red marker‘s imprint.
Solution:
1.Imprints that appear can be automatically repaired after placing here for 3-5 days.
2.Use a film rolling machine instead of manual winding.
3.Strengthen the inspection and remove the imprint on the membrane with alcohol.
Problem 6: Edge fried glue.

Reason:
1.The film cutting knife has been used for too long and has not been replaced in time.
2.Winding process or collided with a hard object during transportation.
Other reasons:
1.Violent logistics.
2.Manual cutting on site.
Solution:
1.Regularly check and replace the film cutter knife.
2.Reinforced inside and outside package.
Problem 7: Dimensional deviation.
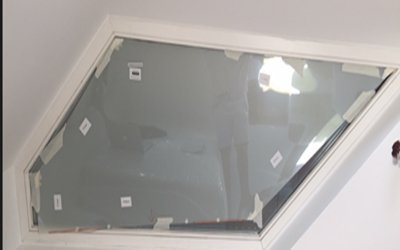
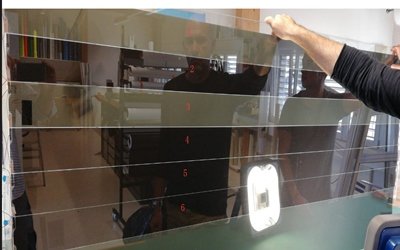
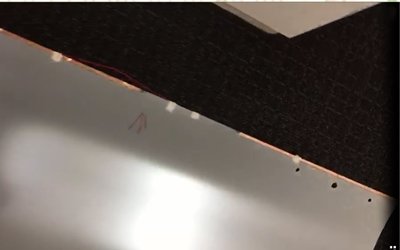
Reason:
1.There is an error on the size of the film.
2.The order color of the film is inconsistent with the delivery color.
3.Incomplete and non-standard busbar making.
Other Reasons:
1.Salesman: wrong order placing.
2.Client: size client provided is wrong.
3.Construction workers: site people wrong measure.
Solution:
1.Print 2 production orders, 2 people cut the film, recheck size.
2.Each step adds a full inspection link to increase the inspection. Check the strength and reduce the error rate.
3.Each production staff maintains a rigorous and serious. Work attitude, enhance communication between departments.
Problem 8: Matters needing attention: packaging, delivery.
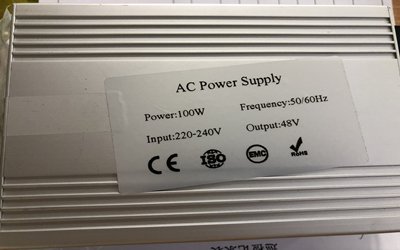

Reason:
1.Labeling is not standardized.
2.The power supply is packaged incorrectly.
Correct Way To Do It:
1.Labels need to be affixed right.
2.Packing power supply: Pearl cotton is used for each power supply separately package, put it in the box after wrapping, inside the box use Pearl cotton . Reinforce the carton after sealing
Power Supply Wrong Packaging Way:
It is forbidden to stack the power supplies directly together and put them in the box.
Construction Link Reasons
Problem 1: How to correctly measure resistance.

Improper Operation:
Place the 2 electric pens on the multimeter on the 2 sides of the copper foil,resulting in the wrong measurement method.
Correct Measurement Steps:
1.Adjust the value of the multimeter (use the small value specification first).
2.Use one electric pen of the multimeter to place it on the copper foil,and the other to place the ITO part that has been sharpened but not coated with silver paste.
3.Check the data, if it does not show, then adjust the data big.
4.Measurement results: If the resistance value is between 150-300 ohms,good conductivity; if the resistance is above 500-1000 ohms, it may periodic poor contact occurs; if the resistance is above 1000 ohms, it does not even the value appears, which proves that the ITO conductive layer may have been burnt down, and the film needs to be replaced, can no longer be repaired.
Problem 2: The film is not sticky.

Reason:
1.On-site environment, high relative humidity and large water vapor.
2.Clean the glass with water before sticking the film, and the water on the glass surface is not removed.
3.When the hand touches the corner of the film during construction, there is sweat on the hand,and the corner is touched many times, resulting in a decrease in the viscosity of the glue at this position.
Solution:
1.Before delivery, it needs to be baked in the oven to remove the moisture around and on the surface of the film.
2.Use a hot air blower to heat the surface of the glass, or turn on the indoor air conditioner.
3.Reduces direct hand contact with the film after the film is in good position.
4.External reinforcement – hot melt adhesive, scotch tape, baffle cover, etc.
Problem 3: Film creases.


Reason:
1.During construction, the method and strength were not paid attention to when peeling the film, resulting in creases.
2.During construction, hold the film in your hand, and use your fingers to push out the marks ,or film hit hard objects.
The Correct Way To Hold The Film:
1.film tiled on a flat surface.
2.Gently roll the film into a tube.
3.After looking at the surroundings, transfer the film to another location.
Other Reasons:
1.Every time taking film out , it is possible to cause film creases.
2.collision.
3.Violent transport.
4.other.
Precautions:
1.The product is fragile and needs to be handled, placed and installed with care.
2.When taking the film, pay attention to the surrounding environment and see if there are any obstacles.
3.During construction, be careful not to touch the frame on the glass, etc.
Problem 4: Film has bubbles.
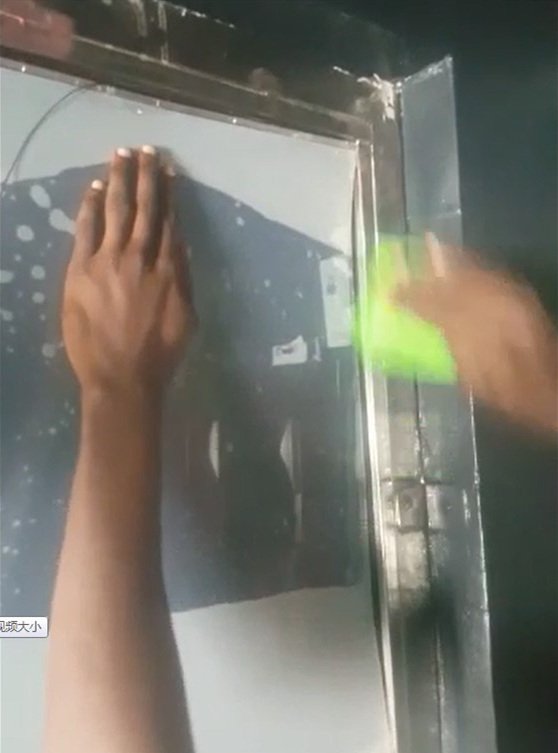
Reason:
1.New construction workers did not correctly grasp the specific operation steps of construction.
2.If the glass is not cleaned completely,there will be many bubbles in the film.
Other Reasons:
1.Site environment has many dust.
2.Use water to paste film.
3.After tearing off the protective film, there are impurities on the adhesive surface.
Glass Cleaning Steps:
1.First wash the glass with water (glass water).
2.Wipe water on the glass with a no dust cloth/paper wipe clean.
3.Wipe the glass surface with alcohol and no dust clothes /paper (Alcohol is volatile, speeding up the removal of moisture at glass surface).
4.Note: There should be no moisture on the cleaned glass.
Problem 5: Puncture.

Reason:
1.After wire connected, short-circuit ignition is caused by the contact between the electrode position and the profile.
2.Film busbar connected to 220V directly.
Other Reasons:
Water entered film from four edges.
Precaution:
1.When wiring, wrap the electrode position with electrical tape to isolate the profile, and seal it with glue.
2.Please check if wire connected right.
Problem 6: Ignition point with diameter over 3mm appear in the middle of the membrane.

Reason:
Wrong wiring leads to excessive voltage so that breakdown film.
Precautions:
1.Wiring Drawings
2.Electrician, professional operation.
Link Of Raw Materials Reasons
Problem 1: AB glue and hard layer.

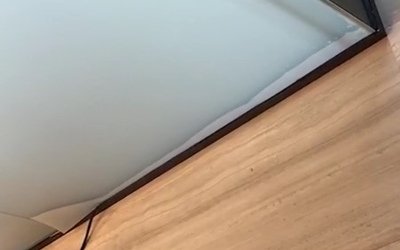
Reason:
1.The viscosity of AB glue is weak.
2.Impurities exist in AB glue and hard layer self side (black spots, small white spots, other lines, etc.).
Solution:
1.Increase the viscosity of AB glue to 12g/in.
2.Strengthen incoming material inspection: check the appearance of the coil surface before cutting the film,pull out any problems films and give feedback to upstream suppliers to solve.
Problem 2: Accessories – power supply.
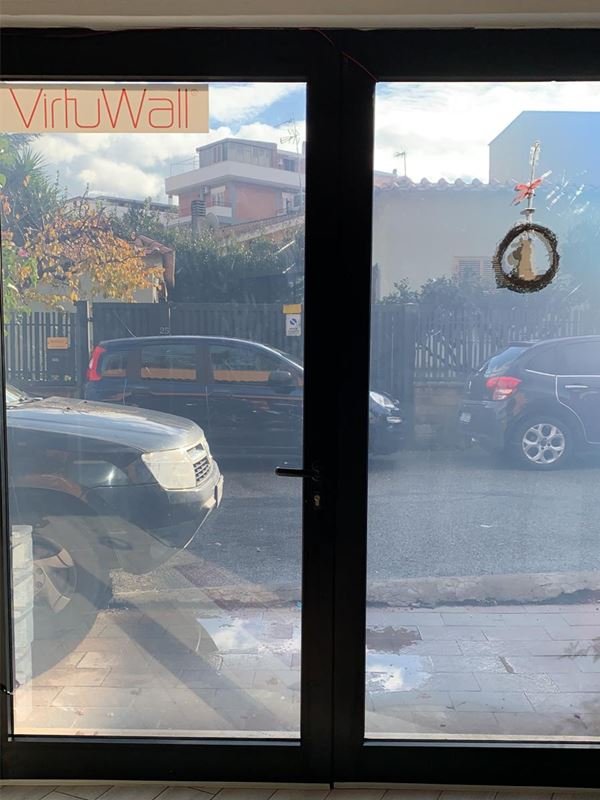

Commen Problems:
1.The remote control is insensitive, garbled, no response or slow response.
2.Power does not work or turns on automatically after transportation
3.The translucency of the membrane after power-on is asynchronous and Low transmittance and high haze.
4.After power on, the film starts to flicker.
5.others.
Solution:
1.Replace or customize a more stable and matching remote control.
2.Strengthen the fixation and matching of the internal plug-in of the power supply.
3.Strengthen the optimization and configuration of the internal circuit of the power supply.
4.It can be solved by FM power supply.
5.others.
Problem 3: Abnormally bright.

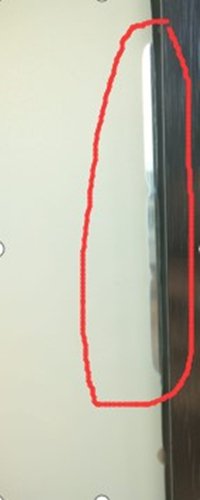


Problem Reflection:
The smart film appears abnormally bright and the liquid crystal layer side shrinks.
Reason:
1.The problem of the material itself is not anti-UV or anti-scratch.
2.Long-term direct sunlight outdoors.
Solution:
1.The front and back sides of the material need to add anti-UV function: acrylic glue + hard film.
2.Try to use indoor rather than outdoor curtain walls or exposed sun rooms.
Operation Link Of Business Personnel Reasons
Problem : Order confirmation error.


Reason:
1.Business personnel are careless, resulting in wrong size, wrong information, and wrong remarks.
2.The information on the order placed by the business personnel was incomplete, and was later handwritten on the production order. The packaging personnel did not see the information, and the added part was not sent out.
Solution:
1.The business supervisor strengthens the training and management of the salesperson, and regularly reviews and controls it at the regular meeting.
2.Business personnel can request construction personnel, supervisors, and colleagues to conduct re-inspection.
Customer Factor Reasons
Problem 1: Partially not bright.

Reason:
Due to the inaccurate dimensions provided by construction personnel, business personnel or customers, the film size is large, and the film needs to be manually cut on site.
Solution:
Wipe the trimmed part with alcohol.